Идея предложена на основании запроса № 18 от 27.01.2023 года с краудсорсинговой площадки изобретателей – Способы восстановления металлов из руд.
Предлагается восстановление железной руды до железа проводить в капельном (1-5 мм) горении специально подготовленной топливно-металлургической водной суспензии. Сжигание топливно-металлургической водной суспензии должно проводиться в классической печи, которая переоборудована для работы на водо-угольном топливе.
Предлагается топливно-металлургическая водная суспензия, как смесь воды с порошком угля и реагентом (железная руда), средним фракционным составом 75-150 мкм.
Ответ на вопрос, сколько железа восстановится за время окислительно-восстановительной реакции горения капли топливно-металлургической водной суспензии – может дать только эксперимент.
В этом случае теоретический расчёт скорости восстановления мельчайших частиц руды на основе известного ступенчатого механизма провести невозможно, т.к. не учитываются размеры и количество частиц руды в капле и т.п. Например, ориентировочный вес одной частицы руды с содержанием 78% оксида железа размером 100 мкм составляет 0,005 мкг и содержит 0,002 мкг железа.
Размер и содержание частиц угля и руды в капле, средний размер капли и время горения в печи будут определять зольность топливно-металлургической водной суспензии, и как результат – выход “губчатого” железа.
Топливно-металлургическая водная суспензия напоминает водо-угольное топливо, только без реагента. Имеет подобный механизм капельного горения.
Механизм капельного горения водо-угольного топлива в топке печи существенно отличается от горения классического жидкого, газообразного или пылевидного топлив.
Капельное горение водо-угольного топлива.
Известно, что водо-угольное топливо (ВУТ) представляет собой дисперсную смесь, состоящую из угля с размерами частиц 75-150 мкм. и воды.
Известно, что при сгорании капель водо-угольного топлива образуются полые сферические частицы более крупного размера, чем исходный фракционный состав водо-угольного топлива.
Известно, что каждая капля водо-угольного топлива в среднем содержит до 200 частичек угля. Практика показала, что при распылении водо-угольной суспензии формируются капли (сфера, эллипсоид и др.) 3-5 мм. При попадании каждой капли водо-угольного топлива в горячую печь сначала вода с поверхности капли мгновенно испаряется. В след за этим происходит испарение влаги внутри капли и одновременное воспламенение микрочастиц угля на поверхности капли. Начинается горение наружных микрочастиц угля капли по следующим схемам:
C + O2 = CO2,
2C + O2 = 2CO,
C + CO2 = 2CO.
Одновременно с процессом воспламенения наружных микрочастиц угля капли проходит другой и самый интересный процесс, в том числе, для заявленных целей восстановления металла из руды. Перегретый пар изнутри капли взаимодействует с углеродом по следующим схемам:
C + H2O → CO + H2,
H2O → H2 + O2.
Образуются восстановители (водород и углерод). Восстановители приводят к более экологическому горению водо-угольной смеси по сравнению с традиционными топливами. Восстановители удаляют почти все оксида азота и серы в уходящих газах за счёт протекания следующих реакций восстановления:
NOx + H2 (СО) → N2 + H2O (СО2),
SOx + H2 (СО) → S + H2O (СО2).
Таким образом, резкому уменьшению образования летучей золы, оксидов серы и азота, способствует классический процесс восстановления оксидов азота и серы водородом и углеродом.
На основании вышеизложенного можно предположить следующее:
ГИПОТЕЗА
Капельное горение топливно-металлургической водной суспензии как одновременный источник тепла и “губчатого” железа в одном технологическом процессе.
Капельное горение топливно-металлургической водной суспензии необходимо проводить в обыкновенной печи, которая переоборудована для работы на классическом водо-угольном топливе. Переоборудование печи заключается в простой замене форсунки, которая позволяет формировать воздушно-капельное облако с средним размером капель в 1-5 мм.
Топливно-металлургическая водная суспензия формируется из порошков угля и реагента – руды со средним фракционным составом 75-250 мкм.
В каждой капле топливно-металлургической водной суспензии в среднем содержится смесь из 100 частичек угля и 100 частичек руды.
При попадании капли топливно-металлургической водной суспензии в горячую печь – сначала мгновенно испаряется вода с поверхности капли. В след за этим происходит испарение влаги внутри капли с одновременным воспламенением внешних микрочастиц угля капли. Перегретый пар внутри капли взаимодействует с углеродом капли, с образованием CO и H2 (восстановитель). Восстановитель, выходя из капли, взаимодействует с частицами руды внутри капли и восстанавливает их до железа, см. рис. № 1.
Этому способствует “лабиринтный” (более медленный) выход восстановителя c вовлечением в реакцию восстановления всех частиц руды.
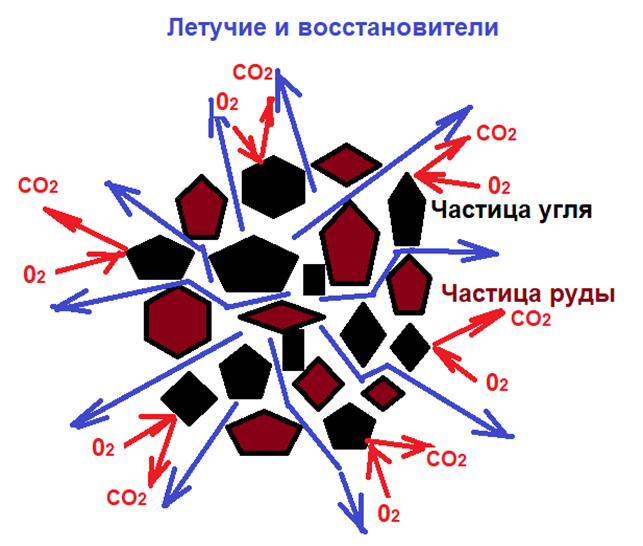
Рис. № 1. Стадия горения частиц угля на поверхности “капли” с выходом летучих и восстановителей (CO и H2).
Необходим эксперимент, подтверждающий предложенную идею, т.к. теоретический расчёт скорости восстановления мельчайших частиц руды на основе известного ступенчатого механизма провести невозможно, т.к. не учитываются размеры и количество частиц руды в капле и т.п.
В этом случае должно быть выполнено условие по верхнему пределу температуры горения топливно-металлургической водной суспензии – не выше 1000 градусов. Необходимо предотвратить начало спекания частиц руды в капле. Температура горения топливно-металлургической водной суспензии определяется процентным содержанием воды, и может соответствовать 850-900 градусов.
ВЫВОД:
- Использование топливно-металлургической водной суспензии в классической печи, которая переоборудована для работы на водо-угольном топливе (оборудована распылителем под заявленный размер капель) – решает две задачи:
– энергетическая – получение тепла для различных целей.
– металлургическая – получение “губчатого” железа в зольном виде.
2. Ответ на вопрос, сколько железа восстановится за время окислительно-восстановительной реакции горения капли топливно-металлургической водной суспензии – может дать только эксперимент.
3. Теоретический расчёт скорости восстановления мельчайших частиц руды в этом случае, на основе известного ступенчатого механизма провести невозможно, т.к. не учитываются размеры и количество частиц руды в капле и т.п.
4. Предполагается, что простой эксперимент может подтвердить заявленную гипотезу. В этом случае, любая тепловая электростанция и ее разновидность – теплоэлектроцентраль (ТЭЦ), при незначительных доработках – превратиться в тепло-электрометаллургический завод. Коксоаглодоменное производство, как основная экологическая нагрузка на природу уйдёт в историю. История технологий производства меди в доказательство сказанному. В древности породу, обогащенную медью, перемешивали с углем и помещали в глиняный горшок. Далее массу в горшке поджигали. Выделяющийся угарный газ восстанавливал породу до меди. По аналогии, все в точности, как сейчас происходит в доменной печи. При этом, металлургия меди вышла на совершенно новый технологический тренд в виде пирометаллургии, гидрометаллургии и электролиза меди. А металлургия железа из прошлого, в виде коксоаглодоменного производства – осталась без изменения.