Опубликована 02.07.2021 года.
Предлагается простейшая технология изготовления объёмных полупроводников для термоэлектрического элемента термоэлектрического генератора с энергетическим выходом 0,2 вольт на 100 градусов.
Полупроводниковый термоэлемент состоит из двух полупроводниковых «таблеток» p-типа и n-типа, не образующих p-n–переход, которые соединены между собой.
Каждая «таблетка» синтезирована методом СВС. Одна «таблетка» — из оксида меди и алюминиевой пудры, вторая «таблетка» — из медного купороса и алюминиевой пудры.
Технология изготовления следующая:
Реактивы:
1) Медный купорос.
2) Натрий двууглекислый или обыкновенная пищевая сода
3) Алюминиевая пудра.
4) Железный купорос
СВС “таблетки” из медного купороса.
Порошок медного купороса перетирается в ступе до пылевидной структуры. Смешивается с алюминиевой пудрой.
Изготавливаем несколько смесей в следующей пропорции (оксид меди: оксид алюминия) 90:10, 87:13, 84:16, 82:18. Это необходимо для экспериментов с получением максимального термо ЭДС для определённого диапазона температур.
Смесь засыпается в стальную толстостенную трубку диаметром 8 мм и прессуется сверху ударами болта М8. Получается классическая достаточно прочная “таблетка” из спрессованной реакционной смеси для СВС. Затем сверху таблетки газовой горелкой инициируется протекание скоростного высокотемпературного синтеза. СВС в данном случае протекает послойно сверху вниз совершенно спокойно без образования пор, разрыхлений и т.п., в полной противоположности классической алюмотермии, примером которой является обыкновенный бенгальский огонь.
СВС “таблетки” из оксида меди.
Оксид меди изготавливается из медного купороса классическим способом. Берётся отдельно сода и купорос в пропорции 1:1 по весу. Далее медный купорос растворяется в воде. Затем в воду добавляется сода. Начнется бурное вспенивание раствора и выделение углекислого газа. Отделяем наш осадок от раствора путем фильтрации (отжимать марлей). Полученный густой продукт небесно-голубого цвета “размазывается ” по стальному листу и прокаливается сверху газовой горелкой до образования чёрного порошка. Получается чистый оксид меди.
Полученный порошок из оксида меди перетирается в ступе до пылевидной структуры. Смешивается с алюминиевой пудрой.
Изготавливаем несколько смесей в следующей пропорции (оксид меди: оксид алюминия) 90:10, 87:13, 84:16, 82:18. Это необходимо для экспериментов с получением максимального термо ЭДС для определённого диапазона температур.
Смесь засыпается в стальную толстостенную трубку диаметром 8 мм и прессуется сверху ударами болта М8. Получается классическая достаточно прочная “таблетка” из спрессованной реакционной смеси для СВС. Затем сверху таблетки газовой горелкой инициируется протекание скоростного высокотемпературного синтеза. СВС в данном случае протекает послойно сверху вниз совершенно спокойно без образования пор, разрыхлений и т.п., в полной противоположности как при классической алюмотермии, примером которой является обыкновенный бенгальский огонь.
СВС “таблетки” из оксида железа.
Оксид железа изготавливается из железного купороса классическим способом.
Берётся отдельно сода и купорос в пропорции 1:1 по весу. Далее железный купорос растворяется в воде. Затем в воду добавляется сода. Начнется бурное вспенивание раствора и выделение углекислого газа. Отделяем осадок от раствора путем фильтрации (отжимать марлей). Полученный густой продукт зеленоватого цвета “размазывается ” по стальному листу и прокаливается сверху газовой горелкой до образования чёрного порошка. Получается чистый оксид железа.
Полученный порошок из оксида железа перетирается в ступе до пылевидной структуры. Смешивается с алюминиевой пудрой.
Изготавливаем несколько смесей в следующей пропорции (оксид железа: оксид алюминия) 90:10, 87:13, 84:16, 82:18. Это необходимо для экспериментов с получением максимального термо ЭДС для определённого диапазона температур.
Смесь засыпается в стальную толстостенную трубку диаметром 8 мм и прессуется сверху ударами болта М8. Получается классическая достаточно прочная “таблетка” из спрессованной реакционной смеси для СВС. Затем сверху таблетки газовой горелкой инициируется протекание скоростного высокотемпературного синтеза. СВС в данном случае протекает послойно сверху вниз совершенно спокойно без образования пор, разрыхлений и т.п., в полной противоположности как при классической алюмотермии, примером которой является обыкновенный бенгальский огонь.
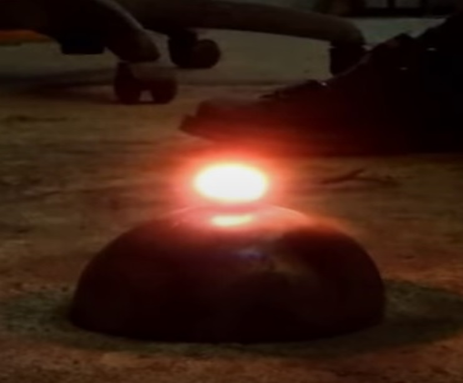
Рис. № 1. Само распространяющийся высокотемпературный синтез (СВС)

Рис. № 2. Объёмные полупроводники, полученные СВС.
Известно, что по виду проводимости полупроводники подразделяют на n-тип и р-тип. У чистых или собственных полупроводников концентрация электронов и дырок одинакова. Электропроводимость собственного (беспримесного) полупроводника очень низка.
Чтобы превратить собственный полупроводник в примесный, необходимо ввести в его кристаллическую решетку некоторое количество специально подобранной химической добавки, т.е. осуществить легирование полупроводника.
Примеси создают ряд энергетических уровней в запрещенной зоне. В результате вероятность образования электронно-дырочных пар при температуре возбуждения оказывается значительно более высокой, чем в собственном полупроводнике.
В таких полупроводниках электрическая проводимость осуществляется в основном за счет носителей зарядов одного знака – электронов или дырок. Чтобы обеспечить электронную или дырочную проводимость, достаточно, как правило, ввести один атом соответствующей примеси на атомов собственного полупроводника.
ВЫВОД:
Показана возможность получения объёмных полупроводниковых материалов методом само распространяющегося высокотемпературного синтеза.
Технология само распространяющегося высокотемпературного синтеза позволяет получать объёмные полупроводники N и P типа любой формы в зависимости от химического состава легирующих примесей в порошковой смеси для СВС